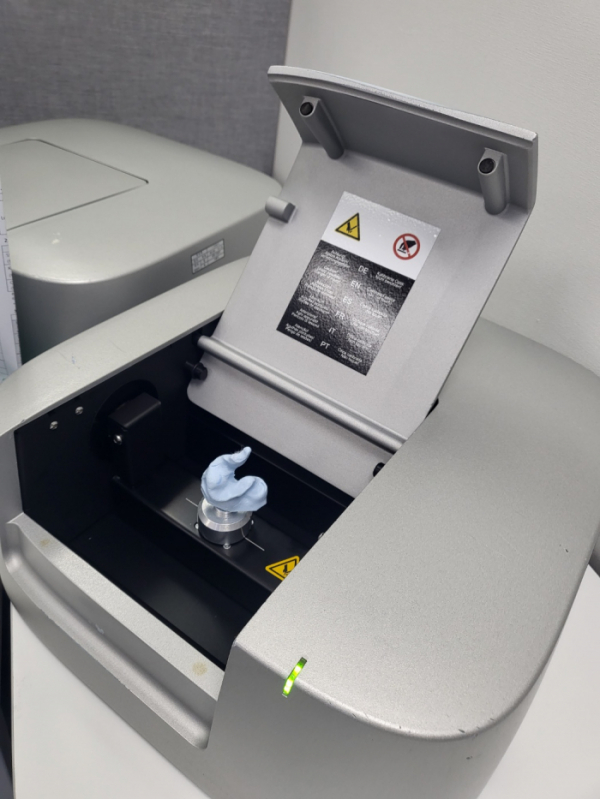
보청기도 패션인 시대다. 과거 투박했던 외형과 달리 최근에는 다양한 디자인과 모양으로 변화하고 있다. 기능적인 면에서도 블루투스를 연결해 음악을 듣거나 통화를 할 수 있도록 진화했다.
19일 관련 업계에 따르면 앞으로 보청기 수요는 더욱 늘어날 전망이다. 급속한 고령화로 국내 노인 난청 인구가 빠르게 증가하고 있기 때문이다. 특히 최근에는 3D프린터를 이용해 자신의 귀에 맞는 맞춤형 보청기도 등장했다.
아시아 단일 국가 내 최대 규모의 보청기 생산시설인 서울 가산디지털단지의 시그니아 가산 오퍼레이션센터를 최근 방문했다. 이곳에서는 시그니아의 3D 프린팅 보청기가 만들어지고, 오픈형, 귀걸이형 보청기의 애프터서비스(A/S)도 제공된다.
가산 오퍼레이션센터 입구에 들어서면 3D 프린팅 보청기 제조공정을 한눈에 보여주는 ‘인터랙티브 월’이 좌측 벽면을 가득 메운다. 월을 통해 단계별 제작 과정을 상세히 알 수 있다. 우측에는 시그니아의 다양한 제품들이 전시돼 있다.
면적 905.3㎡(약 274평)의 센터 내부는 크게 보청기 사용자의 귓본을 취합해 3D 스캐닝과 모델링을 하는 공간, 3D 프린팅 및 조립과 품질검사를 하는 생산실, 전국 각지로 배송하는 물류센터로 등 3곳으로 구분된다. 내부는 다음 공정으로 쉽게 넘어갈 수 있게 동선이 꼬이지 않도록 배치돼 있다.
3D 보청기의 공정 과정은 크게 5단계다. 전국에서 실물 귓본이 도착하면 본격적인 작업이 시작된다. 먼저 배송된 귓본을 3D 스캐닝 작업을 통해 파일 형식으로 변환한다. 이 스캐닝한 파일을 전문가가 3D 모델링 프로그램을 기반으로 보청기의 모양과 내부 공간을 설계한다.
3D 모델링이 완료된 파일을 기반으로 3D 프린터를 사용해 보청기 쉘이 제작된다. 쉘은 프린팅된 잉크가 차곡차곡 쌓여 만들어진다. 완성된 쉘은 조립실로 전달돼 사용자가 원하는 옵션을 프로그래밍한 보청기 키트와 접합시켜 3D 보청기로 만들어진다.
김현백 시그니아 오퍼레이션센터 부장은 “3D 프린팅 보청기는 스캐닝, 모델링을 거치기 때문에 보청기 제작 시간이 단축되고 정확한 측정 기반의 생산이 가능하다”며 “파일 형식으로 변환하기 때문에 다시 제조할 때 바로 사용할 수 있고, 같은 데이터를 사용해 파손 등이나 분실 시 귓본 없이 제작할 수 있다”고 설명했다.
이어 그는 “직접 눈으로 귀 모양과 내부 부품의 위치와 공간 등을 보면서 제작 가능하다는 것이 3D 프린팅 보청기 장점”이라고 덧붙였다.
품질관리(QC) 단계에서는 완성된 보청기의 성능과 외관을 글로벌 기준에 따라 검사한다. 단순히 수치가 맞지 않으면 이전 단계로 돌아가지만, 옵션 자체가 틀리면 처음으로 간다. 검수까지 끝난 제품은 물류센터에서 전국으로 향한다.
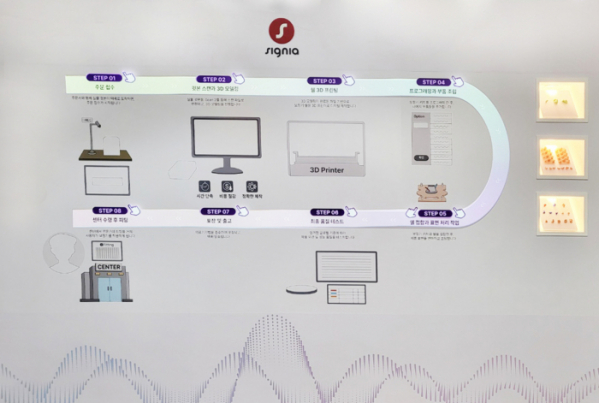
김 부장은 “가산 오퍼레이션센터는 아시아에서 가장 넓고 작업환경이 청결하다. 신속한 작업을 위해 동선이 꼬이지 않도록 만들었다”며 “물류센터에서 모든 프로세스는 자동화, 분업화, 디지털화로 제품 출고부터 배송까지 일어날 수 있는 오류를 줄였다”고 소개했다.
가산 오퍼레이션센터의 특징은 보청기 조립 과정을 제외한 모든 공정이 디지털화된 점이다. 제품 주문이 시그니아의 내부 전사적자원관리(ERP)에 입력되는 순간부터, 제조 과정을 마치고 출고를 위한 패키징이 이뤄지는 모든 과정이 시스템으로 운영된다.
김 부장은 “보청기 업계에서도 3D 프린팅을 포함한 3D 공정을 도입한 업체가 늘었다. 시그니아는 업계 최초로 이 공정을 도입해 오랜 시간 데이터를 기반으로 한 노하우를 보유하고 있다”며 “제조 과정 역시 엄격한 글로벌 R&D 기준에 따라 표준화된 공정에서 제조하고 있다”고 말했다.
이어 그는 “제조의 기본은 품질 컨트롤이기 때문에 이를 위해 지속적으로 역량 강화를 할 것”이라며 “착용자의 만족도를 높이기 위해 노력할 것”이라고 강조했다.