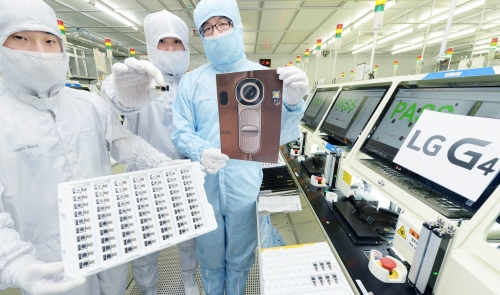
LG전자의 차세대 스마트폰, ‘G4’ 카메라의 심장부를 엿보는 과정은 시작부터 까다롭다. 방진복과 방진화, 방진모, 마스크에 두 겹의 장갑을 착용해야 생산라인으로 들어갈 수 있다. 여기에 일곱 차례의 이물제거 절차를 거쳐야만 비로소 10존 클린룸에 발을 들여놓을 수 있다.
17일 LG전자의 차세대 스마트폰 ‘G4’ 카메라의 심장부, LG이노텍 광주공장을 찾았다. 이곳에서는 G4에 탑재되는 조리개값 F1.8의 1600만 화소 후면 카메라와 전면 800만화소 카메라 모듈을 생산한다. LG이노텍 광주 공장의 자랑은 반도체 생산라인 수준에 버금가는 무결점 ‘10존 클린룸’ 카메라모듈 생산라인이다. 10존은 1ft³(세제곱피트ㆍ약 30cm 길이의 정육면체 크기)의 공간에 0.0005mm 크기의 먼지가 10개 이하인 상태를 뜻한다.
이렇게 출입관리가 까다로운 것은 최고의 품질 상태를 유지하기 위해서다. 혹시 모를 공기중의 작은 먼지 하나라도 제품에 들어가게 되면, 스마트폰으로 촬영할 때 화면에 작은 점처럼 보이는 불량 카메라모듈이 나올 수도 있기 때문이다. 손톱만한 크기의 카메라모듈을 만들기 위해 작업자들은 그야말로 먼지와의 사투를 벌이고 있는 셈이다.
생산라인에는 먼지를 완벽하게 제거할 수 있는 시스템이 곳곳에 숨겨져 있다. 천장과 바닥에 설치된 특수장치가 압력을 가해 생산라인에 있을지도 모르는 먼지가 날아다니지 않게 한다.
LG이노텍 관계자는 “이곳에서 오랜 기간 일하는 작업자들의 경우 쌀 한 가마에 버금가는 압력을 어깨로 받고 있다”며 “고산지대에서 사는 것과 같은 압력이 작용한다”고 말했다.
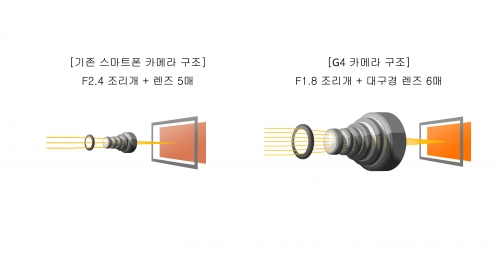
이곳에서 생산되는 모든 카메라모듈은 반드시 양산 테스트를 거친다. 각각의 제품은 자동화된 테스트 장치를 통해 오토포커스, OIS(손떨림보정기능), 해상도 등을 점검한다. 이 혹독한 과정을 거쳐야만 비로소 G4의 부품이 될 수 있다. 특히 OIS기능 품질 테스트를 위해 수십 대의 검사장비 안에 카메라모듈을 넣어, 수백 번을 흔들면서 촬영하는 가혹 테스트를 진행하고 있다. G4 사용자가 일상생활에서 사진을 찍을 때, 손이 떨리는 상황을 가정한 테스트 공정이다.
G4에 탑재될 1600만 화소 카메라를 개발하는 데 걸린 시간은 약 1년 남짓. 핵심공정만 3개월간의 과정을 거쳐 원점부터 재설계했다. 급격히 성장하고 있는 스마트폰 카메라 시장에 선제적으로 대응하기 위해서다. 스마트폰 카메라 시장은 2009년부터 꾸준히 증가하기 시작해 2013년을 기점으로 생산량이 10억대를 돌파했다. 올해를 기점으로 15억대 수준에 이를 것으로 전망된다.
LG이노텍은 약 3개월간의 과정을 거쳐, ‘어드밴스트 액티브 얼라인’공정을 개발했다. 이 공정은 6겹의 대구경 렌즈가 겹쳐진 ‘경통부’와 ‘이미지 센서’를 결합하는 핵심 공정으로 기존 ‘액티브 얼라인’ 공정보다 정밀도를 40% 향상시켰다.
이와 함께 LG이노텍은 G4의 내부 공간에 800만 화소 전면카메라 모듈을 넣기 위해 0.11mm 두께의 초박막 ‘글래스타입 블루필터’를 적용했다. 이를 통해 모듈 전체의 두께를 4.46mm로 초슬림화하는 데 성공했다.
유동국 LG이노텍 카메라 모듈 개발팀 책임연구원은 “스마트폰과 함께 양분화 돼 있던 기존 DSLR 시장 등은 연구 인력이 축소되고 있는 상황”이라며 “스마트폰용 카메라 기능 향상으로 시장 영역이 확대될 것으로 보인다”고 말했다.
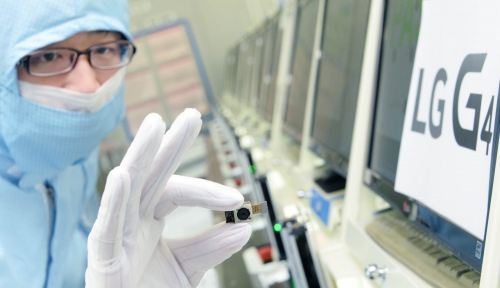