지난 7일 방문한 경기도 화성시에 위치한 탄탄한 강소기업 동구바이오제약 공장은 크게 생산동과 연구동, 물류동으로 구성돼 있다. 공장 답사의 백미가 복잡다단한 공정을 살펴보는 데 있다면, 취지에 가장 적합한 공장은 바로 제약 공장임이 분명하다. 그만큼 생산단계가 복잡 다단하기 때문이다.
180여 종 품목 제약의 연구 설계가 진행되는 연구동에서 출발해 생산동으로 이어지는 동구바이오제약 공장도 그랬다. 수십 개의 공정들이 각각 배치된 작은 방들이 꼬리에 꼬리를 물고 연결돼 있었다. 이곳에서 우리에게 친숙한 알약들이 하루에도 수십만 정씩 반죽돼 찍어져 나오고 있었다.
회사 관계자의 설명에 따르면 이 생산 라인은 2014년 리모델링을 거치며 훨씬 더 복잡했던 공정들을 선진국 기준에 맞춰 개편한 것이다. 조용준 동구바이오제약 대표는 수출의 단계적 확대란 목표에 맞춰 과감한 설비 투자를 거듭해왔다. 그는 이날 기자들에게 “올해 여름에는 중기청의 스마트공장 사업 지원을 받게 돼 입출고와 생산 전반에 걸쳐 공정이 더욱 전자화되고 효율화될 예정”이라고 귀띔했다.
연구동의 중앙실험실과 품질보증실에는 각각 22명과 11명의 연구원이 개별 과정을 맡아 연구를 진행하고 있다. 연구실장은 “중앙실험실에 입고된 원료는 검체를 체취한 후 무게를 달고 전처리 과정을 거쳐 시료의 불순물과 위험물질을 걸러내 용매와 가스의 품질적합 여부를 판정하는 단계를 거친다”며 “생약 제재나 액체약은 추가로 미생물실험실에서 미생물 검출 테스트를 거쳐야 한다”고 설명했다. 이렇게 개발 단계부터 십수가지의 엄격한 검증을 완료한 신제품만이 비로소 생산에 들어갈 수 있다.
생산동 출입 절차는 연구동보다 까다로웠다. 우선 갱의실에서 위생복과 위생모, 위생신으로 갈아입고 다시 덧신과 마스크를 착용하는 절차를 거쳐야만 출입할 수 있다. 생산동에서는 약물이 딱딱한 알약의 형태인지, 캅셀(캡슐)의 형태인지, 연질 캡슐의 형태인지에 따라 다시 별도의 라인으로 분리된다.
농축된 액체가 젤라틴 피막에 주입돼 말랑말랑한 연질캡슐은 동구바이오제약이 기술 우위를 보유하고 있는 대표적 부문이다. 설비 투자와 기술력이 요구돼 생산 방식이 까다롭기 때문에 국내에서도 3~4군데의 제약사만이 연질캡슐을 대량생산할 수 있다. 회사는 자사의 연질 캡슐약뿐만 아니라 타사 약품까지 ODM으로 납품하는 등 연간 3억여 정의 연질 캡슐을 제조한다.
이날 방문한 생산동에서는 이 연질캡슐이 생산되는 공정을 관찰할 수 있었다. 교반, 분쇄, 탈포의 복잡한 과정을 거쳐 농축된 액체 약물과 젤라틴을 녹여 만든 피막액을 성형실에서 합쳐야 비로소 연질캡슐이 탄생했다.
알약 생산의 경우 과립은 정제를 통해 체적을 줄이고, 혼합과 건조 과정을 차례로 거쳐 타정실로 이동한 후 반듯한 알약의 모양으로 성형돼 나왔다. 타정실에서는 시간 당 20만 개의 속도로 수십 만 개의 알약이 생산된다고 했다. 이 알약은 정제 선별실로 이동해, 불량 선별과정을 거친다. 16개의 카메라가 각기 다른 각도에 배치된 선별기가 사진을 찍는 동시에 조금이라도 깨진 곳이 있으면 별도의 필터로 분리했다. 선별된 알약은 코팅실에서 달달한 필름으로 코팅된 후 레이저 인쇄실에서 한알 한알 고유번호를 부여받고는 종합포장실로 이동해 포장된다.
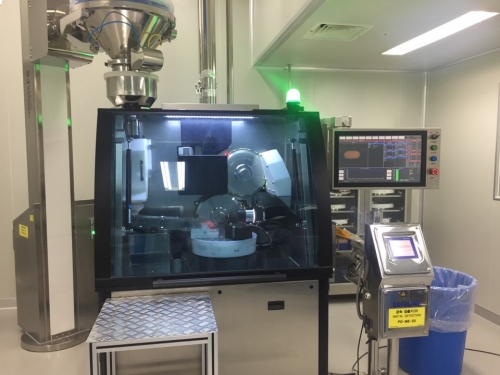
여타 공장처럼 컨베이어 벨트를 이용하는 대신 각각의 과정이 별도의 방에 분리된 까닭은 동구바이오제약이 대량생산 대신 다품종 소량 생산을 지향하기 때문이다. 각 방에서는 연구원들이 오가면서 기계들의 생산을 관리하고 있었지만 이미 대부분의 공정이 자동화돼 있었다. 올해 47년차에 접어든 탄탄한 강소기업 동구바이오제약이 200명 남짓의 인력만 가지고도 874억 원의 연매출을 올리며 업계의 신뢰를 쌓아온 배경에는 이렇게 공정과 R&D부문에서의 지치지 않는 투자와 혁신 노력이 있었다.