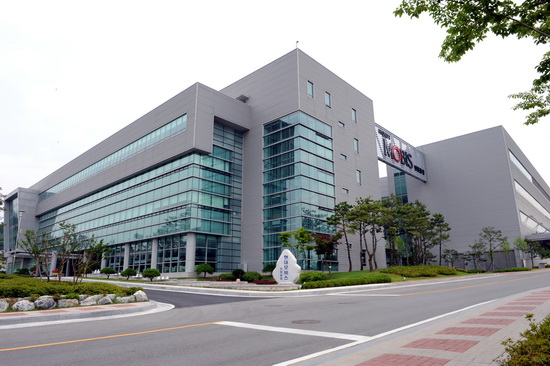
고속도로를 한 시간 남짓 달려 도착한 충청북도 진천. 현대모비스 진천공장이 위치한 곳이다. 공장에 들어서니 시원한 녹음 속에 푸른 유리장식이 멋스럽다. 자동차 부품 공장이라고 하면 으레 비산먼지와 소음을 떠올리게 마련이지만 현대모비스는 이 같은 고정관념을 무색하게 만든다.
진천공장은 현대모비스가 신성장동력으로 육성하고 있는 전장부품 전문공장이다. 진천공장에서는 오디오와 AVN 등의 멀티미디어 부품을 비롯해 에어백 제어 유닛, 차선이탈경보장치, 하이브리드 차량용 ECU 등 다양한 전장 제품을 생산하고 있다. 지난해 6월 현대오토넷과의 합병을 통해 진천공장은 현대모비스의 시스템 및 전자부문의 핵심 거점으로 떠올랐다.
지난 2008년 2월 준공한 진천공장은 연간 AVN 42만대, 오디오 110만대, 전장품 550만개를 생산한다. 주요 생산품을 전시해놓은 쇼룸을 거쳐 생산라인으로 이동했다. 정전기와 먼지에 민감한 전자 부품을 생산하고 있는 만큼 생산라인에 들어가는 절차도 까다롭다. 정전기를 최소화한 제전복과 제전화로 갈아입는 것은 기본이고 생산라인에 들어가기 전 신발 바닥에 묻은 먼지를 제거하고 에어샤워로 먼지를 제거한 뒤에야 비로소 생산현장을 둘러볼 수 있었다.
작업자들을 살펴보니 푸른색의 팔찌를 각각 착용하고 있다. 살펴보니 머리 높이의 전선과 이어져 있다. 특수 처리된 바닥과 접지시켜 작업자의 몸에 남은 정전기를 지속적으로 제거하는 장치란다. 이 밖에도 라인 곳곳에 화분과 어항을 설치해 습도를 조절함으로써 정전기 발생을 최소화하고 있다. 습도는 40~60%, 온도는 섭씨 23~25도 안팎으로 유지해 제품 품질에 대한 외부 영향을 줄이고 있다.

1층 라인에서는 회로기판에 부품을 삽입하는 작업 중이다. 자동화 6개 라인에서 월간 6400만 건을, 수동 6개 라인에서 월간 18만건의 작업을 진행한다. 간단한 기판은 자동화라인으로 커버되지만, 첨단 부품일수록 회로기판이 복잡하기 때문에 수동라인에서 작업한다.
1층에서 조립된 회로기판은 2층으로 옮겨져 완제품으로 태어난다. 2층 생산라인에는 총 37개의 조립라인이 있는데 오디오 8개 라인에서 월간 9만 대, AVN 9개 라인에서 월간 3만5000대, 전장 16개 라인에서 월간 46만대의 제품을 생산한다. 엄격한 공정 관리에 걸맞게 설비도 최신화돼 있어 일부 라인의 경우 20m가 넘는 작업 라인에 투입되는 인원이 2명에 불과하다.
3층의 성능시험실에서는 멀티미디어 제품의 성능과 동작, GPS/DMB 및 메카트로닉스 제품을 실제 동작시켜 성능을 측정한다. 전원시험실에서는 정전기 및 전원이 끊겼을 때 발생할 수 있는 제품의 전기적 변동을 측정하고, 내구시험실에서는 실제 사용하는 것과 같은 상태에서 발생할 수 있는 문제점을 확인한다. 이 같은 철저한 품질 관리를 통해 불량률은 100만개 중 9개 수준으로 유지되고 있다. 작업현장에 걸린 모토 '아름다움의 극치는 정확'이라는 말이 와닿는다.
진천공장은 올해 25만대의 AVN을 생산할 예정이다. 지난해 대비 43%나 증가한 것이다. 오디오는 약 244만대로 작년보다 19% 늘어난 물량을 계획하고 있다. 국내에서 생산되는 K5 K7 YF쏘나타 등과 향후 출시될 그랜저 후속모델, 미국 앨라배마와 조지아 공장에서 생산되는 차종에 장착될 AVN과 오디오 부품이다. 물론 미국에 수출되는 차종에도 공급한다. 마이크로소프트사와 공동개발한 UVO오디오시스템도 생산할 예정이다. 여기에 전장품 620만대 분량이 추가된다.
전장부품 관련 시장이 2010년 1400억 달러, 2015년 1920억 달러로 급속히 성장할 것으로 예상됨에 따라 현대모비스도 전장 분야에 대한 핵심역량 강화에 전력을 다하고 있다. 이에 따라 현대모비스의 전장부품 핵심 메카인 진천공장은 인근에 위치한 덕산공장과 중국의 천진공장과 함께 전장품사업의 큰 축을 담당할 예정이다.
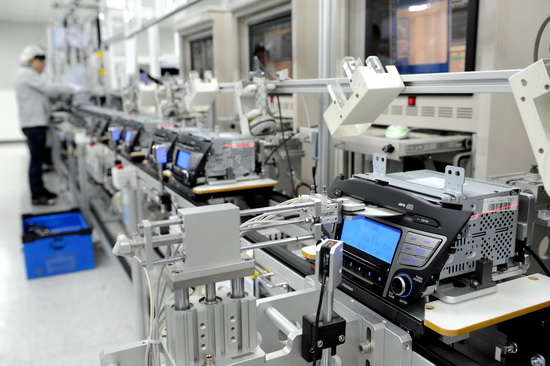