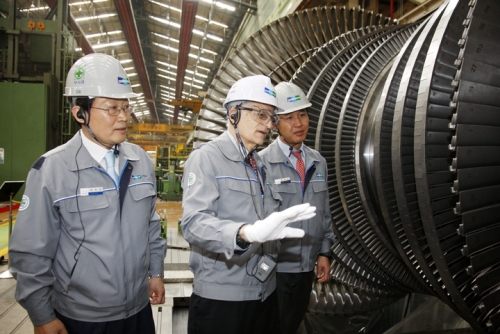
두산중공업은 주·단조 공장과 원자로, 터빈등의 발전설비를 제작하는 가공공장 등을 보유하고 있다. 이 곳에선 커다란 쇳덩이가 치밀한 가공과정을 거쳐 원자력 발전기의 핵심 설비등 최첨단 제품으로 탈바꿈한다.
뜨거운 열기와 둔탁한 굉음이 울려퍼지는 단조공장에 들어섰다. 주조공장에서 공정된 커다란 쇳덩어리들은 단조 공장에서 쓰임에 맞게 가공되고 있었다.
단조공장은 현대화·대형화된 대장간으로 볼 수 있다. 공장에 들어서자마자 새빨갛게 달궈진 소형 자동차 만한 쇳덩이가 눈에 들어왔다. ‘쿵 끼이익 쿵 끼이익’ 커다란 쇳덩어리를 다듬어 원자로의 몸체를 만드는 작업이 한창이었다.
커다란 프레스 옆에는 두꺼운 방화복을 입은 근로자들이 긴 막대기를 들고 굵은 땀을 흘리고 있었다. 1300도까지 열을 받은 쇳덩이는 국내 최대 규모인 1만3000톤의 프레스 기계에 의해 절단된다. 이때 프레스가 누르는 힘은 성인 남성 70만명이 동시에 누르는 힘과 맞먹는다. 쇳덩이에 1300도까지 열을 가하는 이유는 모양의 변형을 좀 더 수월하게 하기 위해서다. 작업 도중 온도가 900도 수준으로 떨어지면 작업을 멈추고 쇳덩이에 다시 열을 가하는 작업을 반복한다.
최남수 두산중공업 단조공장 공장장은 “2~3차 가열을 통해 작업을 끝내는 경우가 대부분이지만 쇳덩이가 클 경우 9~10차까지 작업이 진행되기도 한다”며 “모든 작업은 자동화 시스템을 통해 기계가 하지만 최종 치수 확인은 사람이 직접 고온의 쇳덩이에 다가가 수작업으로 해야 한다”고 설명했다. 지난 50여년 간 최신 공법으로 작업을 간소화했지만 사람의 손이 하는 ‘장인정신’만은 아직까지 이어지고 있는 셈이다.
이렇게 공을 들여 단조작업을 완료한 원자로의 몸체는 가공, 용접 품질검사를 통해 세계 최고의 원자력 설비로 탈바꿈한다.
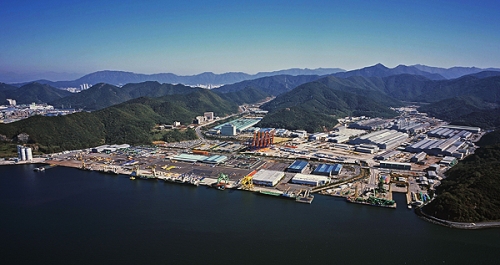
공장은 원전용 터빈 부품 제조에 한창이었다. 터빈 제조 기술의 정수는 블레이드(날개)에 집약돼 있다. 때문에 블레이드를 손질하는 엔지니어들의 작업은 한 치의 오차도 허용되지 않는다. 터빈공장 끝자락에 이르자 로터(터빈 회전축)에 수 백개의 블레이드를 꽂아 연결해 놓은 터빈들이 출하를 기다리고 있었다.
출하 전 블레이드에 쏠리는 모든 진동(부하)을 최소화하기 위한 강도 높은 검수작업은 필수적이다. 공정이 완료된 터빈은 진공상태의 독립적인 방에서 검사를 받는다. 조립이 완료된 터빈은 최신 전투기 빠르기인 마하 2.5의 속도의 회전력을 가해도 아무런 문제가 없어야 출하가 가능하다.
두산중공업은 지난 2009년 증기터빈의 원천 기술을 보유한 체코의 ‘스코다파워’를 인수해 이 분야에서 경쟁우위를 점하고 있다. 원준연 두산중공업 터빈 발전기 생산1팀 상무는 “두산중공업은 고객사가 요구한 치수에서 한치의 오차도 허용하지 않으면서 최단기간내에 생산해 낼 수 있는 터빈생산 기술력을 보유하고 있다”고 강조했다.
마지막으로 들른 원자력 공장에서는 원자로의 모습을 제법 갖춘 원자력 설비들이 막바지 작업에 한창이었다.
현재 원자력 공장에는 우리나라 최초의 원전 수주 프로젝트인 아랍에미리트(UAE)에 브라카 원전에 들어갈 원자력 설비들이 조립을 기다리고 있었다. 오는 10월 원자력 종주국인 미국에 납품될 ‘AP1000’도 늠름한 자태를 뽐냈다.
두산중공업 원자력 공장은 소재에서 최종 조립까지 모든 공정을 한 공장 안에서 처리할 수 있는 일괄생산시스템을 구축하고 있다. 이를 통해 연간 3.5기의 원전 주기기 생산능력을 지난해 5기까지 증대시키며 생산성을 더욱 확대했다.