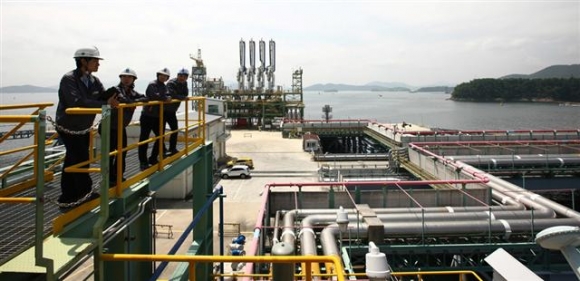
해외에서 LNG를 수입해 소비처에 안정적으로 공급하는 한국가스공사는 생산성 향상을 위해 천연가스 판매가격의 90%를 차지하는 액화천연가스(LNG) 도입단가를 낮추고 가스 생산과 공급설비 운영 효율화를 추진하고 있다.
LNG 구매비용을 최소화하고 설비운영 효율화로 에너지 비용을 절감해 올해부터 3년간 1926억원 규모의 생산성을 높인다는 계획을 세웠다. 여기에 재고자재 회전율을 올해 90.27%에서 2017년 91.65%까지 높여 자재비용을 절감하기로 했다.
앞서 가스공사는 지난 2011년 에너지업계 최초로 에너지경영시스템(ISO 50001)을 도입해 부문별로 에너지 사용량을 관리하고 있다. 이를 통해 에너지 절감 요소를 파악할 수 있게 돼 설비를 교체하거나 설비운영 방법을 개선하고 있다. 특히 소비처에 가스를 공급하고자 감압하는 과정에서 발생하는 폐압을 활용해 전력을 생산하는 등 버려지는 에너지를 활용하는 노력도 아끼지 않고 있다.
노동생산성을 높이려고 자원개발 전문인력을 양성하고 현장을 중심으로 인력을 운영할 계획이다. 공사는 지난 2010년부터 산업인력관리공단에서 인증한 천연가스 설비운영 및 유지보수에 대한 ‘사내기술자격제도’를 도입해 운영 중이다. 이를 통해 현장설비 담당인력의 기술 수준이 향상돼 그동안 외부 기술진에 의존했던 기술감리 등을 자체 수행할 수 있게 됐다.
지난해 31.5%였던 사내기술자격 취득률은 2017년까지 36,7%로 높인다는 계획이다. 이와 함께 현장 생산성을 강화하고자 현장인력 비율도 3년 후 73,8%까지 끌어올리기로 했다.
가스공사는 지식활동 참여가 생산성 향상을 이끈다는 측면에서 직원 누구나 자유롭게 지식 개발을 위한 학습공동체 COP(Community Of Practice)도 만들었다. 이를 통해 아이디어를 현실화하고 우수 지식이나 COP 결과물 등을 활용할 수 있도록 지원한 결과, 매년 큰 비용을 절감하고 지적재산권(기술특허 등)을 확보하는 성과도 거두고 있다.
지식생산성 측면에선 기술개발 성과물을 현장에 적용해 사업화를 강화해나간다는 방침이다. 가스공사는 연구개발을 통해 터미널 및 저장탱크 설계기술, LNG선 화물창 원천기술을 사업화해 경영 개선 성과를 이끌어내고 있다. 그동안 해외 유수의 엔지니어링 업체에 의지해 오던 터미널 기초설계와 저장탱크(14만㎘형, 20만㎘형, 27만㎘형) 설계를 국산화한 것이 대표적이다. 또 LNG선 화물창에 대한 원천기술은 프랑스 GTT사가 독점하고 있었지만 가스공사는 기술력으로 한국형 LNG선 화물창(KC-1)을 개발하기에 이르렀다.
가스공사 관계자는 “이 같은 연구 성과를 통해 비용절감뿐 아니라 지속적인 대내외 수익창출 기반을 마련할 수 있게 됐다”면서 “앞으로 모든 분야에서 혁신 및 지식활동을 통해 2017년까지 2640억원의 생산성을 창출해 나가겠다”고 말했다.